Have Your Cake, and Eat It Too
During my third summer internship with General Motors, I completed a stint in the Lower Structures, Advanced Technical Work group. At the time, our team had been given the directive to complete the upfront development work on what would be the industry’s first carbon fiber-composite pickup bed. Within my initial week on the job, I attended the first crash test of the preliminary tech in which I assisted in analyzing. It was at this point that I had been given the assignment to create and execute tests on the materials to scope improvements. Additionally, the objective was to come up with potential novelty applications that these new materials and executions could enable. This project went on to be part of the newly released 2019 GMC Sierra pickup truck, as the CarbonPro™ Pickup Box and MulitPro™ Tailgate.
Using carbon fiber/composite material was lucrative due to its high strength and durability, yet low weight, as we estimated a total savings of 30kg over the previous generation box. It was an innovative way to set the vehicle apart from the competition, while also increasing performance. A drawback that we incurred was attaching a multi-directional layered composite bed to a solid metal frame, as the two traditionally use vastly different fastening strategies that are not compatible. I cannot fully disclose the solution strategies that we came up with; however, the test procedures that I conducted included: lap shear, tension & cross-tension, wedge peel, drop tower, and adhesive testing. Of course confirming safety was our primary objective, but also understanding the material for innovation opportunities was imperative as well.
Thus, the other half my project included studying what this new material meant for the box’s corrugation patterns from both an aesthetics and functionality perspective. Within my studies, I soon started coming up with more potential ways of taking advantage of the versatile material. For example, we could stamp or layer the composite in many more shapes than capable with metals. Below, you can see some of my initial concept generation, including removable tailgate workbenches, interchangeable subwoofer/speaker system, tool storage, and a special refrigeration package.
I remember during the following semester, having to miss classes in order to take remote patent review meetings. Although some of my specific patent work did not end up panning out, it was gratifying to have my projects influence the direction of the final product available today. For example, as you can see in the upper right figure below, we carried over and developed an embedded tailgate audio system (not seen optioned in the video). Some of our biggest challenges of the MulitPro™ tailgate were those of packaging, weight, and durability; however, our mixed material strategy made it all possible. Thus in this case, we made sure the customer could have their cake, and eat it too.
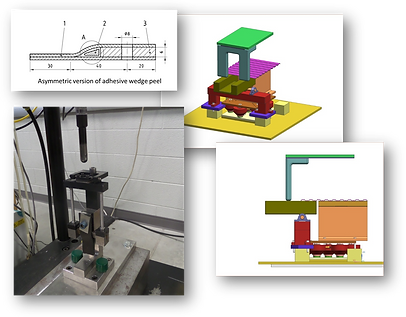
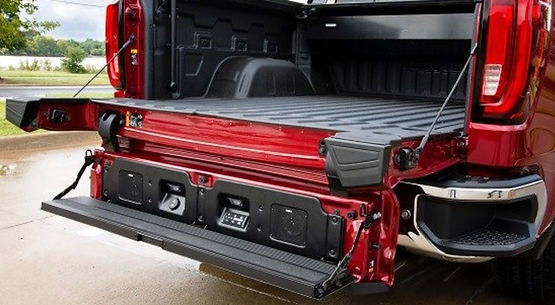




